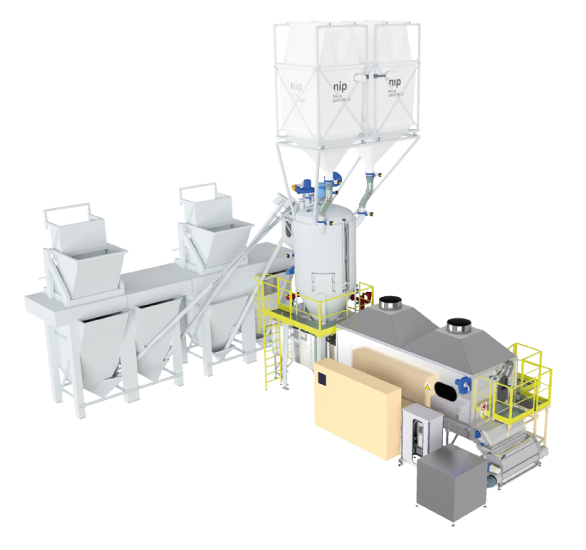
Конический циклический вспениватель
Особый «инструмент NIP» для экономии средств при вспенивании гранул !
С момента презентации этой инновационной технологии в 1998 году было произведено 350 машин.
Главные преимущества заключаются в конической форме и люке для разгрузки материала, расположенном снизу камеры.
- Более толстый слой материала при загрузке сырья (узкий диаметр на дне камеры, даже в моделях большого объёма).
- Снизу камеры образуется большая поверхность для подачи пара при диаметре отверстия от 600мм до 800мм, в зависимости от размера машины. Идеально подходит для работы с сырьём с невысоким содержанием пентана, что позволяет обеспечить подачу большого количества «холодного пара (=пара при низком давлении)» за короткое время при небольшой скорости подачи, таким образом, создаёт более прогрессивный и равномерный процесс вспенивания . В результате мы определённо получаем более равномерное распределение плотности вспененного материала.
- Очень быстрый и естественный способ разгрузки через отверстие внизу камеры: сокращает время цикла и снижает риск перемешивания материала из последующих циклов.
Современная и Прогрессивная система управления
- Контроль процесса при помощи производственных рецептов
- Новая система остлеживания процесса на основе WinCC с 19” (19-ти дюймовым) промышленным сенсорным экраном и персональным компьютером с SSD диском производства Siemens.
- Система контроля производства полностью интегрируется с программным обеспечением Клиента по управлению предприятием.
- Удалённое управление для технической поддержки
При наличии соответствующих опций комплектации позволяет производить как2-ое так и 3-е вспенивание.
Для вспенивания белого и серого материала в одной и той же машине, технология оптимизирована и позволяет минимизировать перемешивание материала из разных циклов.
Предлагаются
- Модели для производста формованых изделий и производства маленьких блоков, которые могут также работать при высоком давлении до 2.5 бар (сертифицированы TÜV) для вспенивания помимо стандартного EPS и Arcel, также EPP или специальные материалы, требующие более высоких температур.
МОДЕЛЬ |
Камера вспенивания с полезным объёмом |
Производительность in 1st Expansion при 18 кг/м3. |
Производительность в 1-ом и во 2-ом вспенивании при 8 кг/м3. |
---|---|---|---|
PJX 400 D | 0,4 m³ |
300 ÷ 340 кг/ч |
76 ÷ 85 кг/ч |
PJX 800 D | 0,8 m³ |
576 ÷ 648 кг/ч |
144 ÷ 160 кг/ч |
PJX 1500 D | 1,5 m³ |
1.080 ÷ 1.224 кг/ч |
272 ÷ 304 кг/ч |
PJX 2000 D | 2,0 m³ |
1.440 ÷ 1.620 кг/ч |
376 ÷ 408 кг/ч |
- Модели для заводов с производством блоков среднего и большого размеров
МОДЕЛЬ |
Камера вспенивания с полезным объёмом |
Производительность in 1st Expansion при 18 кг/м3. |
Производительность в 1-ом и во 2-ом вспенивании при 8 кг/м3. |
---|---|---|---|
PJX 3000 D | 3,2 m³ |
2.178 ÷ 2.448 кг/ч |
536 ÷ 600 кг/ч |
PJX 4000 D | 4,2 m³ |
2.718 ÷ 3.024 кг/ч |
648 ÷ 728 кг/ч |
PJX 5000 D | 5,4 m³ |
3.276 ÷ 3.600 кг/ч |
816 ÷ 920 кг/ч |
PJX 6000 D | 6,2 m³ |
3.654 ÷ 4.014 кг/ч |
888 ÷ 1.000 кг/ч |
PJX 8000 D | 8,0 m³ |
4.320 ÷ 4.716 кг/ч |
1.040 ÷ 1.160 кг/ч |
Мы можем предложить Конический циклический вспениватель в полном соответствии
с производственными требованиями клиента !
Камера поточной сушки для работы в циклическом режиме спроектирована соответствующим образом и предусматривает:
- Избыток вентиляции позволяет материалу быстро дышать
- Специальное «трапециевидное сечение» обеспечивает необходимый поток воздуха вокруг гранул
- Для лучшей обработки гранул поступающий воздух подогревается за счёт конденсата от линии подачи пара.
- Для мягкого и нежного обращения с материалом разгрузка происходит через разделительное сито, а затем через поворотный клапан.
В зависимости от квалификации оператора управление машиной может происходить в одном из режимов по выбору
- В «базовом режиме» с упрощённым вариантом цикла вспенивания, состоящего из меньшего количества фаз процесса.
или
- В «режиме эксперта», с бὀльшим числом доступных фаз для настройки различных параметров цикла вспенивания (давление, % открытия заслонки выпуска, скорость вращения мешалки, кол-во воздуха, подмешиваемого в пар для снижения температуры пара при изготовлении высоких плотностей).
Отслеживание процесса вспенивания
- “Базовый” вариант с возможностью пошагового отслеживания перехода между различными фазами цикла подачи пара за счёт определения уровня вспенивания материала с помощью фиксированным и ещё более эффективным «Вибрационным датчиком уровня». Каждая машина оборудована одним Вибрационным датчиком максимального уровня. Возможна комплектация дополнительными датчиками, которые позволяют управлять переходом от фазы к фазе цикла вспенивания при достижении определённого объёма, а не по времени.
- “Расширенный” вариант выражается в возможности дополнить базовый вариант лазерным датчиком, установленным на линейной оси, на окне камеры, способным «следовать и определять» в реальном времени уровень, на котором находится материал во время вспенивания и позволяет машине постоянно и непрерывно отслеживать происходящее в камере.
Эта опция комплектации называется “Автоматический контроль вспенивания” и даёт машине возможность выравнивать возможную неоднородность сырья, а в результате обеспечивает точность при производстве определённой плотности материала в серии последовательных циклов вспенивания.
Методика определения соответствия полученой плотности производственному заданию
- Система автоматического контроля плотности в базовой версии с отбором 1 пробы из камеры поточной сушки. После определения веса система, при необходимости, автоматически регулирует вес материала следующего цикла (во время фазы взвешивания-калибрования сырья).
- Система автоматического контроля плотности в версии для высококвалифицированных пользователей с отбором 3-х проб из камеры поточной сушки по сравнению с базовой версией, позволяет достичь более высокую точность при определении веса, за счёт учёта среднего значения из 3-х отобранных проб в каждом цикле После определения веса система, при необходимости, автоматически регулирует вес материала следующего цикла (во время фазы взвешивания-калибрования сырья), также, как и в базовой версии.
Допуск расхождения по уровню плотности до ± 1%
Установка может комплектоваться также
- Дополнительными бункерами для загрузки сырья различного качества
- Автоматическими опрокидывателями октабинов (контейнеров с сырьём)
- Системами автоматической очистки для упрощения использования нескольких цветов и видов сырья
- Легким доступом в камеру поточной сушки, упрощающей чистку с помощью специального отсасывающего устройства.
- Вторым и третьим вспениванием: за счёт загрузки через отдельный пред-загрузочный бункер заранее вспененного материала, который может быть вспенен повторно, используя при этом все технологические преимущества циклического вспенивателя.
- Инвертером (для вентилятора) для регулировки скорости загрузки материала в бункера на больших расстояниях.
- Устройствами для точной дозировки красящих порошков или добавок к гранулам пенополистирола в процессе вспенивания
- Программным обеспечением для наглядной визуализации и управления непосредственно с контрольной панели вспенивателя и компьютера в виде синоптической диаграммы всего производства и направления потоков свежевспененного и вторичного материалов, а также системы бункеров.
Также предлагаются Цилиндрические наклонные вспениватели непрерывного действия, только для второго и третьего вспенивания.
- Также предлагаются Цилиндрические наклонные вспениватели непрерывного действия, только для второго и третьего вспенивания.
- Модельный ряд таких машин состоит из PJX 1000 C, PJX 1200 C и PJX 1600 C для производственного объёма в пределах 1000 ÷ 1600 кг/ч при плотности 8 кг/м³.